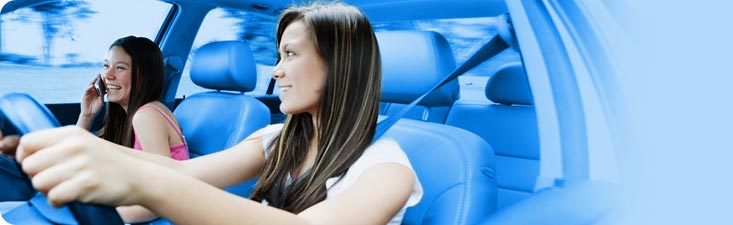
Micronas Develops Dual-Plate Hall Sensor for Automotive Applications (0106)
Freiburg, Germany - April 2, 2001 - Micronas (SWX: MASN, Neuer Markt Frankfurt: MNSN) announced it has successfully integrated two Hall plates, the specific sensor elements, on a single Hall sensor chip at about half the cost of existing solutions. The new HAL 700 family of sensors is designed for contactless detection of speed and rotary direction in automotive applications such as sliding roofs, windshield wipers, seat adjusters and power windows.
Previously, measuring speed and direction meant that systems manufacturers had to meticulously align two separate Hall sensor chips at precisely the required distance and position. Integrating two Hall-plates on one chip instead eliminates this error-prone alignment process, which significantly increases overall system reliability. The one-chip solution also eliminates the need for external logic circuitry and will cost about 50 percent less than two independent sensors.
"The benefit of Hall sensors over conventional mechanical methods is the ability to detect speeds and positions without physical contact," said Ronald Gampp, market manager sensors at Micronas. "This makes sensors immune to mechanical wear and environmental contaminants such as dirt, vibration and great temperature variations, resulting in a much higher level of reliability, which are especially crucial in applications relevant to car and passenger safety."
The two integrated Hall plates enable a sensor to detect if a wheel or shaft moves forward or backward by detecting the magnetic fields of multi-polar, rotating ring magnets. Because Micronas added logic circuitry in its HAL 710 sensor, it can measure both speed and direction of the rotation without the need for external logic circuitry. The on-chip circuitry determines the direction and speed in which the permanent magnet rotates and transmits the information through the output pins.
Hall sensors based on silicon technology supply very low signal voltages. To amplify those low voltage levels without distortion, the offset has to be kept to a minimum. The solution Micronas developed to address this problem was the chopper compensation technique, which constantly rotates the current flowing through the Hall plate. Micronas' sensors create a pure measured value by rotating the direction of the current about 100,000 times per second. The result is a very precise device, with maximum two percent deviation, that can function flawlessly over a temperature range of -40F (-40°C) to 284F (+140°C) with strong long-term stability.
The HAL 700 and the HAL 710 are available in 4-pin SOT89B packages. Prototypes are currently available and high volume production will start in the fourth quarter of this year at prices below US $0.50 for volume orders over 500,000 units.
About Hall sensors
Hall sensors are based on the Hall effect, named after its discoverer Edwin Hall in 1879. A Hall element, a square shaped semiconductor layer, for example, is supplied by a constant current. When applying a magnetic field perpendicular to the current flow, the charge carriers are deflected due to the Lorentz force. This deflection can be measured as the so-called Hall voltage, which is perpendicular to both the magnetic field and the current flow. The Hall voltage is directly proportional to the magnetic field.