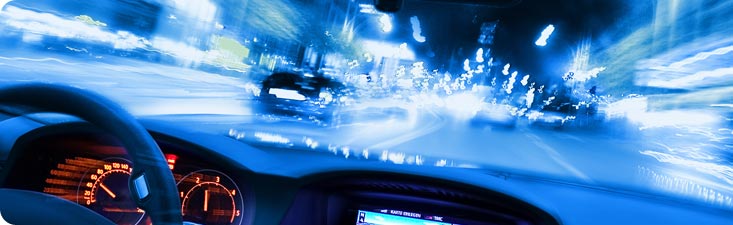
About Hall sensors
The Hall effect
The function of a Hall sensor is based on the physical principle of the Hall effect, which was named after its discoverer, Edwin Herbert Hall (1855-1938): If a magnetic field takes affect perpendicular to a current-carrying conductor, an electrical voltage is created across the current flow direction (Hall voltage).
During the Hall effect, when applying a magnetic field perpendicular to the current flow, the electrons are deflected to the edge of the sensitive element due to the Lorentz force. A potential difference is therefore created: the so-called Hall voltage. This voltage is proportional to the field strength of the magnetic field and the current strength of the acting current. A wide range of applications are offered by utilising this proportionality. As such, the strength of an external magnetic field can be defined. Current measurements are also possible as each conductor through which current flows creates its own a magnetic field. This magnetic field can now be used to (indirectly) measure the current.
Since the Hall effect is most pronounced in semiconductors, typically a small plate of semiconductor material is used as the Hall element.
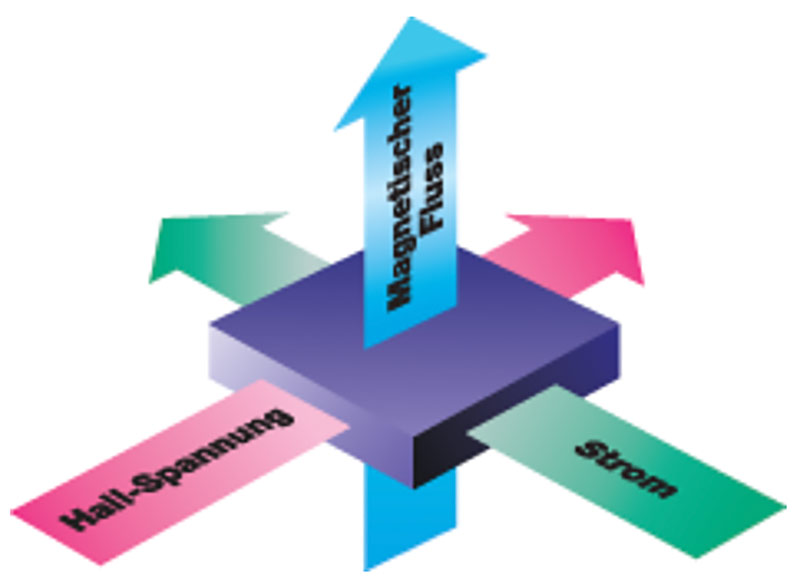
The Hall effect: In a semiconductor Die, the Hall voltage is generated by an external
magnetic field acting perpendicular to the current direction.
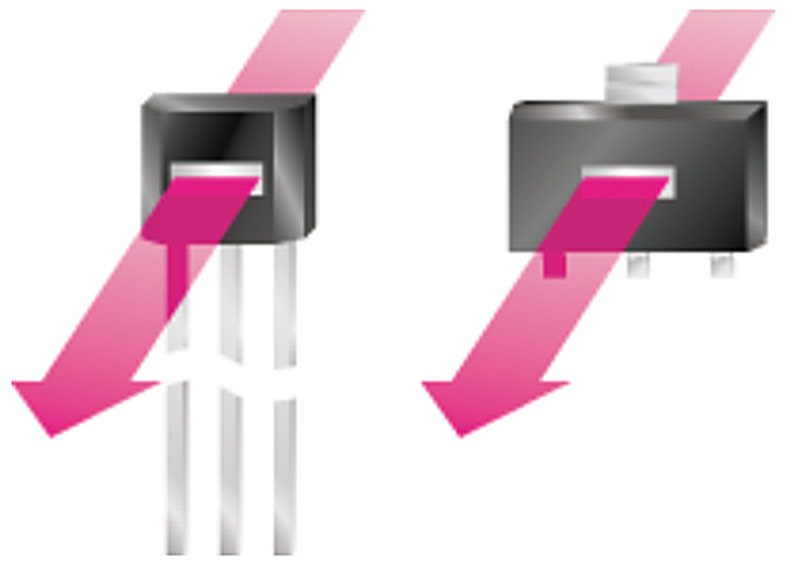
CMOS Hall sensors leaded and in SMD package.
The component of the magnetic flow is measured vertically to the chip surface (arrows).
In today’s Hall sensors, the required evaluation electronics are normally integrated on the chip together with the Hall plate. Field lines that penetrate the Hall element vertically generate a proportional electrical voltage, which is processed by a digital signal processor and converted into a usable output format.
From Hall element to mixed-signal IC
The first CMOS-based Hall sensors were pioneered and developed by what is now TDK-Micronas in the early 1990s. As the manufacturing process became cheaper, the ICs could be better integrated, allowing the design of more complex circuits. Now, digital and analog functions are combined on the same chip as mixed-signal integrated circuits.
Nevertheless, major challenges needed to be overcome before a CMOS Hall sensor could be realized. One reason behind this: Hall sensors operate at very low signal voltages. They are therefore prone to offset drifts that can occur as a result of temperature and voltage fluctuations, as well as mechanical stress, such as transmitted from the housing to the chip. External influencing factors considerably distort the low measurement signal. Such factors also need to be compensated, in order to gain a precisely and reliably working Hall sensor.
TDK-Micronas made a breakthrough with the chopper method, also known as “active offset compensation”. The concept involved continuously (“choppering”) switching the current direction through the Hall plate to the actual sensor Die. To do so, the voltage supply and taps for the Hall voltage were attached diagonally to the square Hall plate. Distortions in the measurement signal, which for example are formed due to geometric distortions of the Hall plate, enter into the measured value in the same strength regardless of the current direction, but are either added or subtracted depending on the current direction. Since both measurements are performed using identical structures with the same stress profile, the offset caused is evened out over the mechanical housing voltages.
In the next step, engineers turned to the operational amplifier. It was possible to limit the offset across the entire operating temperature to a few µV and considerably improve the EMC and voltage stability of the circuit. The foundations were thus laid for a complete CMOS Hall sensor system that includes on-chip signal processing and non-volatile memory integration.
Once the offset problem had been solved, TDK-Micronas started to market the first robust and thermally stable Hall switches and linear Hall sensors in CMOS technology. The following developments include high-precision angle sensors based on internal 3D HAL® technology. By using both vertical and horizontal Hall plates, multidimensional magnetic field measurements are now possible: Vertical Hall plates detect magnetic field lines parallel to the sensor surface, while the horizontal Hall plate detect the vertical component impinging on the chip surface.
This is crucial for use in the automotive industry which requires tighter integration and EMC optimization of components in automotive designs. It resulted in the development of sensors with integrated decoupling capacitors as well as sensors which must meet the Functional Safety requirements of ISO 26262. In safety-critical applications, high reliability can be achieved with the help of the redundancy principle. TDK-Micronas offer sensor solutions here, which include two independent semiconductor chips in a single package.
Robust and resistant Hall sensors
Hall sensors with integrated decoupling capacitors
In addition to the technical ongoing development which spans several generations of Hall sensors, new concepts are being implemented, which are specially developed with the stringent requirements of modern vehicles in mind. The motto in automotive electronics is “robustness” and “noise immunity”. With this in mind, TDK-Micronas has launched EMC-resistant sensors with integrated decoupling capacitors. The capacitors are integrated into a transistor package within close proximity of the sensor chips and are therefore very well placed to keep away from interference pulses of the semiconductor Die. This solution does not require any external components, is cost-effective, space-saving and highly efficient.
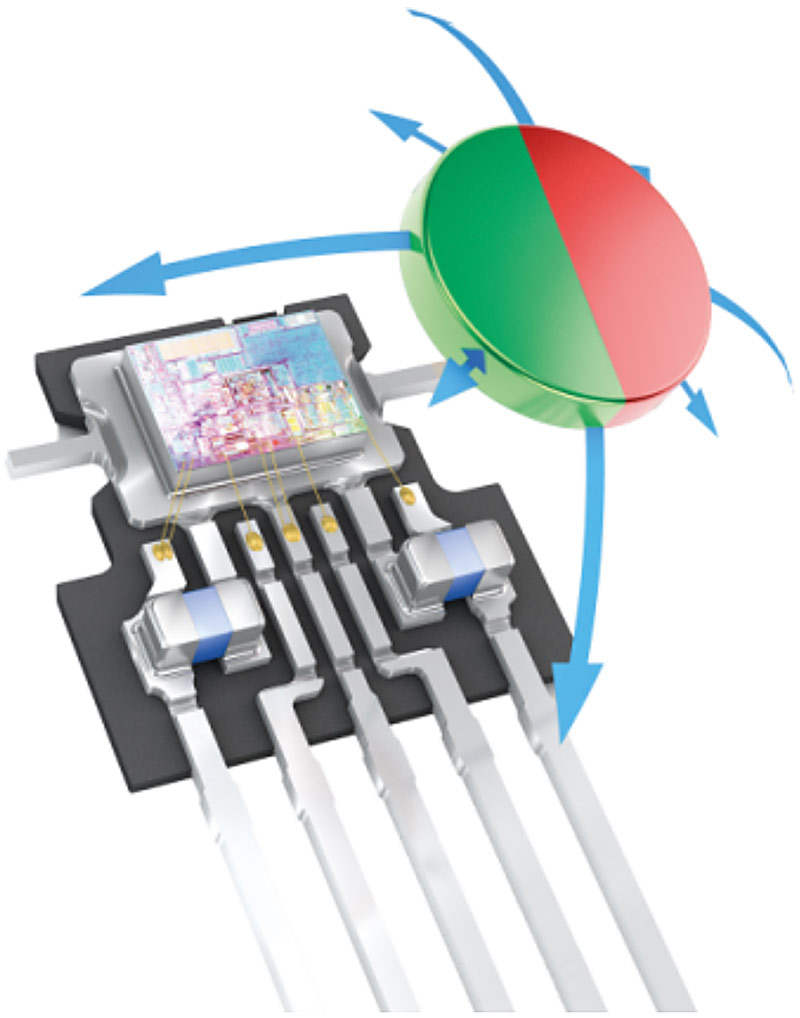
Sensor solution with integrated decoupling capacitors for multidimensional magnetic-field measurement
Hall sensors with redundancy function (Dual-Die solution)
Safety-critical automotive applications such as drive-by-wire systems call for additional functionality protection. This is where the redundancy principle comes into its own, which was applied in the early days of avionics. The thinking behind it: Components are installed several times and operated in parallel. The output signals are continually compared in the case of identical input signals. If these signals deviate to an intolerable extent, a fault is present and predefined measures can be taken, such as starting an emergency program. A solution was found for Hall sensors from TDK, which makes using a second component a thing of the past: Two independent sensor Dies are integrated into a single SMD package. They are arranged vertically to ensure that they are penetrated by the same magnetic fields and therefore provide the same output signals. A lower offset is, however, unavoidable for bonding the bond wires – it can be disregarded though.
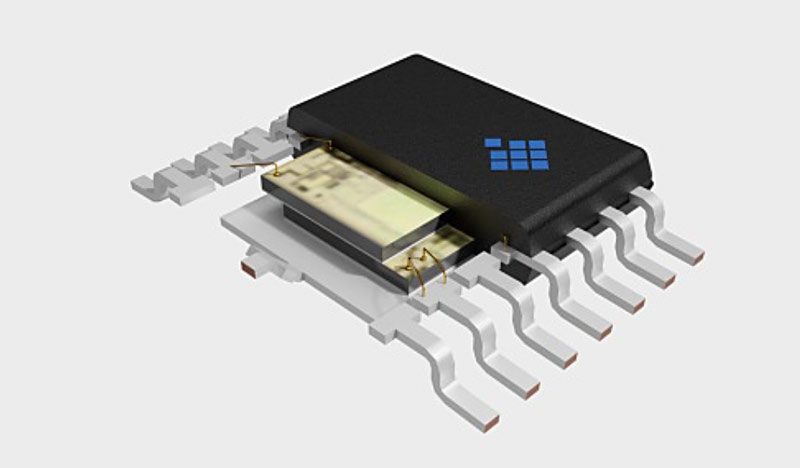
Dual-Die Hall sensor with redundancy function for safety-critical applications in the automotive industry
Hall-effect sensors and their applications
A large number and variety of sensor applications can be implemented in automotive and industrial electronics using Hall sensors from TDK − from the commutation of brushless electric motors (BLDC), to the indirect measurement of electrical current through to the precise measurement of steering angles.
The combination of Hall sensor and permanent magnet allows a host of variables such as rotational speed (RPM), angle, rotation, fill level, pressure or torque to be measured. Compared to other technologies, Hall sensors have the advantage that they are not sensitive to dust, contamination or water, provided they are optimally enclosed. As they make no physical contact with the object being measured, they experience virtually no wear and are therefore extremely reliable.
Hall sensors are used for position detection, among other things, in which the precise measurement of a distance or angle is required. Thanks to their high level of precision and robustness, Hall-effect sensors are well suited for use under the engine bonnet, where they can reliably work at ambient temperatures of up to 160°C.
Hall switches
Functional principle: When a magnet is brought near to the sensor, the measured magnetic field strength is compared with a threshold value. As soon as this value (switching point) is exceeded, the switching status changes at the output of the sensor which, depending on its type, exhibits unipolar, bipolar or latch-switching behavior.
TDK-Micronas offers the HAL 15xy switch family herewith predefined characteristic values. It was designed primarily for automotive applications and meets requirements for functional safety. All members of the HAL 15xy product family are defined according to the ISO 26262 standard as SEooC (Safety Element out of Context) ASIL B-ready. This switch is available in TO92 or SOT23 cases as a 3-wire or 2-wire version. The latter has a current source output and therefore only needs two supply cables. Typical applications in the automotive industry include detecting the brake fluid level, detecting whether safety belts are fastened or use as a brake light switch. Hall switches are increasingly replacing conventional microswitches, for example in seat belt buckles or blinds. Moreover, they can be used in combination with a motor controller for the commutation of brushless electric motors.
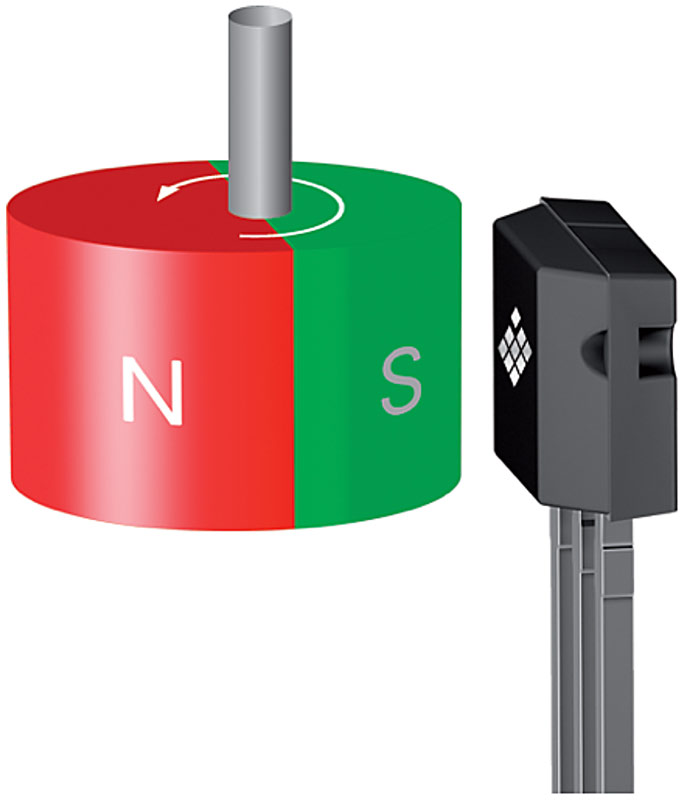
Speed measurement by Hall switches
Linear Hall-effect sensors
Path measurements or the measurement of rotary movements require the more complex Hall sensors with linear output characteristics, which output a signal that is proportional to the magnetic field strength. This output signal can be provided as an analog voltage, a pulse width modulated signal (PWM) or in the form of a modern bus protocol (e.g. SENT). The output characteristic can be linearized with the aid of as many as 32 grid points. This enables tolerances of the magnets or of the mechanical design to be fully compensated. The HAL 24xy sensor family has diagnostics capability and was designed for precise distance measurement up to 40 mm and for angle measurements up to 180 degrees. Designed for use in particularly safety-critical drive-by-wire applications, the HAR 24xy sensor variant can offer a redundancy function. In this case, two independent sensor chips (Dual-Die) are integrated into a single TSSOP package. Typical applications include magnetic field measurements and the substitution of conventional potentiometers that are prone to wear. In vehicle applications linear Hall sensors are used in particular for detecting pedal positions or steering torque, where they are increasingly being replaced in these applications by direct-angle sensors.
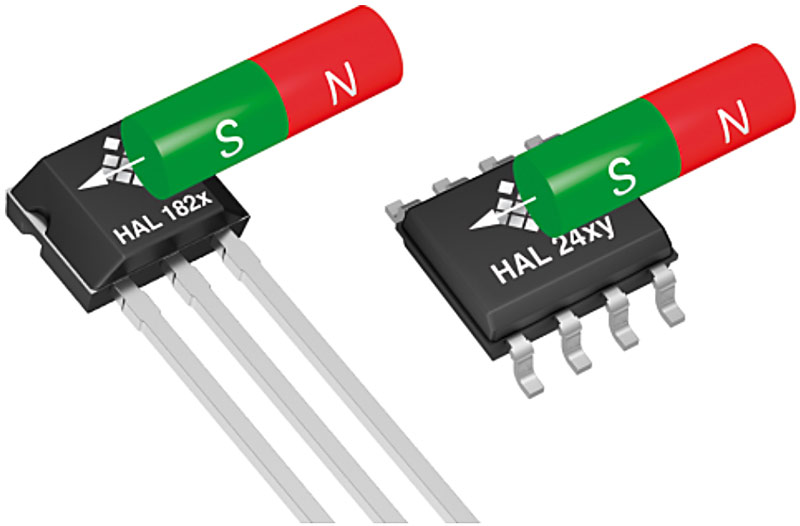
Defining position and movement with linear Hall sensors
Direct-angle sensors
While linear scale sensors measure only the amplitude of a magnetic field, direct angle sensors are also capable of capturing the field vector. The magnetic field component perpendicular to the chip surface is recorded by both types of linear scale sensors. The “vertical” Hall elements of the 3D sensors also detect the magnetic-field component in the chip plane. From this, the internal signal processing calculates angle and position information, which is output as an analog, PWM or bus protocol output signal (e.g. SENT).
The HAL 39xy sensor family from TDK-Micronas uses internal 3D HAL® technology and at the same time is resistant to external magnetic interference fields. The unique concept is based on a series of Hall plates. Each measurement mode uses another Hall-plate combination to gain the best test result. The highly flexible sensor array of the masterHAL® sensor line helps design engineers select the best operation mode for any given measurement task. The HAL 39xy sensors are the only system solutions available on the market, which integrate all four modes in a single sensor. They create a clear advantage for customers, as only one component needs to be qualified rather than several different hardware versions. The new sensors are suited to a wide range of applications, including all types of valves and actuators, gear shifters, pedal position, gear position, steering angle or chassis position detection.
In addition to the output characteristic, major characteristics can be adjusted to the magnetic circuitry by programming the non-volatile memory. The HAC 39xy is equipped with integrated capacitors, meeting stringent EMC requirements and eliminates the need for a PCB, thus reducing the total system size and cost. HAR 39xy is the dual-die version of the HAL 39xy series. Typical applications include very precise measurement of magnetic-field alignment or linear movement of up to 40 mm and angular range of up to 360°. Direct-angle sensors are ideally suited to detecting the position of the throttle valve or clutch pedal.
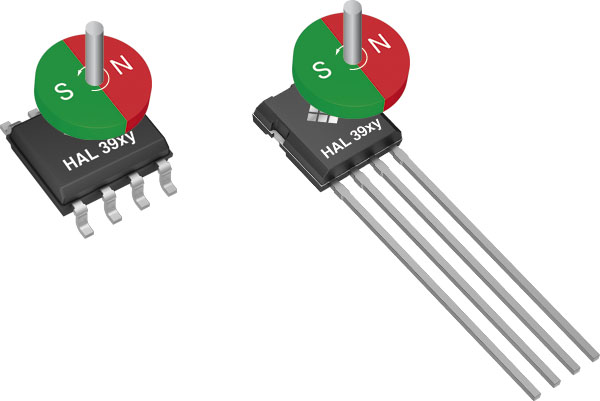
Measuring direct angles with 3D-Hall-sensors