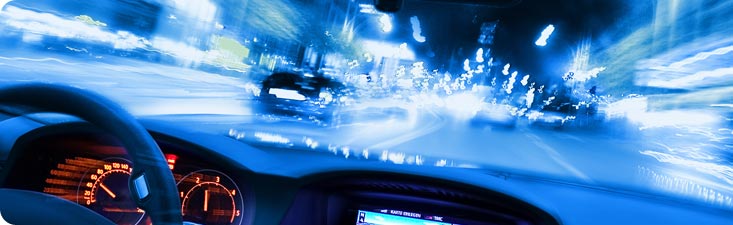
Magnetic Field Sensors – Tunnel Magneto Resistive (TMR)
The Tunnel Effect: TMR measurement principle
Tunnel magnetoresistive (TMR) technology is based on a quantum mechanical effect. In a magnetoresistive effect (MR), a magnetic field change leads to a change in the electrical resistance. As a result, a magnetic field and electrical variable can be measured based on their relation to one another. TMR is a special form of MR technology where, the so-called tunnel effect ensures a much greater change in resistance as soon as a magnetic field is applied. As a result, TMR sensors offer the advantage of higher sensitivity and accuracy.
In TMR sensors, a stack of magnetic material is separated in the middle by an electrical insulator - the so-called tunnel barrier. The direction of the magnetization of the free layer depends on the external magnetic field. The direction of the solid layer remains unchanged. The resistance of the TMR element is proportional to the relative angle between free and solid layers.

Fig. 1: Functional principle of TMR technology
TMR, AMR, GMR: Technology comparison
Modern TMR sensors grew out of AMR (Anisotropic Magnetoresistive) technology and GMR (Giant Magneto-Resistance) technology which was also developed during the early 1990s. Compact components based on these technologies led to the adoption of microscopic MR read heads in hard drive and away from larger electromechanical heads, allowing for higher storage density. With the further development of TMR technology that utilized a manufacturing process similar to that of a CMOS, different layers are deposited and patterned on a silicon wafer. Consequently, TMR resistance elements are connected serially to form a resistance element. These resistors are usually arranged in groups of four, as a Wheatstone bridge circuit. This type of interconnection generates common electrical signals in automotive technology that can be evaluated directly or by means of downstream electronics (ASIC IC).
The rate of change in the resistance of an element is expressed by a value called the MR ratio. The MR ratios of conventional AMR elements and GMR elements are about 3% and 12% respectively. In contrast, the MR ratio of a TMR element is 100%. In a GMR element, in which a non-magnetic metal (Cu, etc.) is sandwiched between two ferromagnetic layers, electron transfer occurs as electric conduction in the metal. In a TMR element, on the other hand, electron transfer occurs as a quantum mechanical tunnel effect. For this reason, when the pin layer and free layer are in an antiparallel, a TMR element has an extreme characteristic in which electrons "cannot move almost at all," when compared to the characteristics of a GMR in which "it is hard for electrons to move." This causes a TMR element to exhibit an extremely large MR ratio, in addition to giving a distinctive character to its output, such as "Yes or no" or "1 or 0."
Moreover, this is also the reason why TMR elements are utilized as highly-sensitive reading element in HDDs today. Therefore, by using these highly-sensitive TMR elements as magnetic sensors, extremely large output can be obtained. In fact, the outputs of TDK TMR sensors reach 3,000 mV, which is 20 times larger than those of AMR sensors and 6 times larger than those of GMR sensors. Fig. 3 is a comparison of the characteristics of magnetic sensors using an AMR element, GMR element, and TMR element (when a voltage of 5 V is applied).
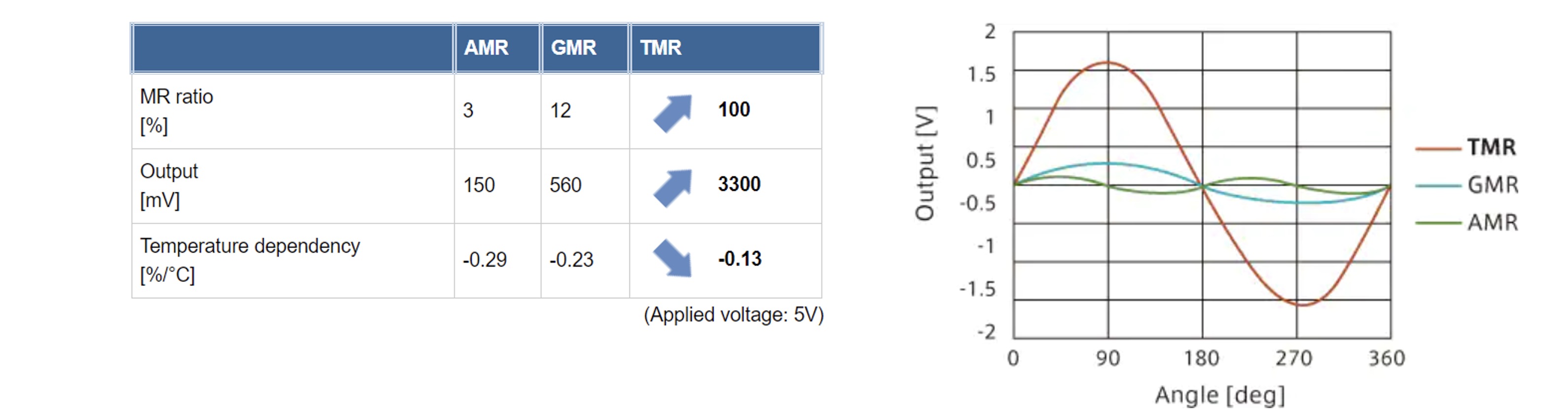
Fig. 2: Comparison of the characteristics of magnetic
sensors using an AMR element, GMR element, and TMR element
TMR sensors for automotive applications
TMS sensors can operate stably under a wide range of temperatures. Because of this, they are increasingly used as automotive components, which require high precision and reliability. They also feature low power consumption and are used in a broad range of products in addition to automobiles including consumer products such as robots and smartphones.
A key parameter for automotive applications is the sensor output voltage which can be read directly from conventional microcontrollers, and as a result, additional amplifier circuits, resistors and capacitors can be eliminated. TMR-based angle sensors, speed sensors and linear sensors can be used to realize power steering systems, wipers, clutch and gearbox actuators, pedals and throttle valves and many other engine and position applications. The simple design of a TMR sensor has many advantages inlcuding more reliabilty resulting in better fuctional safety, and superior monitoring of sensor behavior during operation.
TMR sensors can be used in accordance with ISO standard 26262 to the highest level of safety (ASIL D level) in the automotive industry. Thus, they meet the safety standards to be installed, for example, in electric power steering and brakes. Another important feature is the very high angular accuracy that can be achieved with TMR sensors. Depending on the magnetic field strength, an angular accuracy of up to approx. 0.2 degrees can be achieved during the vehicle's lifetime (17 years) and in the permitted chip temperature range (-40 °C to 175 °C). This performance is reflected in the increase in efficiency and noise reduction, especially for the control of electric brushless DC motors (BLDC).

Fig: 2: Automotive application examples for TMR sensors
Excurse: Hall effect sensor or TMR sensor?
When determining which type of sensor should be used in automotive applications, the special properties of each should determine their usage.
CMOS Hall sensors feature cost-effective monolithic Hall element and transmitter integration on a single chip. This makes them ideal for cost-sensitive applications or for detecting stronger magnetic fields.
Compared to magnetic field sensors based on other technologies (Hall / AMR / GMR), TMR sensors have a better signal-to-noise ratio and score with unprecedented accuracy and very low power consumption. TMR sensors offer reliable and stable performance over temperature and the lifetime of the sensors. As a result, TMR sensors are preferred in very demanding applications.
In many cases, the combination of both technologies can also be very beneficial. For example, in a current sensor module, a TMR sensor can measure weak electric currents while the Hall sensor detects high currents. The measuring range can thus be extended significantly with increased measuring accuracy. A second application for the use of both technologies is determining the rotor position in a brushless electric motor (BLDC). In this case, a high-precision TMR sensor can be combined with a redundant Hall sensor to increase the overall system reliability up to ASIL-D level. In this application, there would be no need for an angle encoder.
Regardless of whether a Hall Effect sensor or TMR sensor or both are used, the technologies in each type of sensor can reduce the overall bill of materials and costs in an automotive design when compared to using other dedicated sensors. By better understanding the technology and applications of each type of sensor, engineers are better able to make informed decisions resulting in safer, more reliable designs.
Contributing to eco-driving as rotation sensors or current sensors in the future
TDK was the first in the world to commercialize automotive TMR sensors and began shipments in 2014. TDK’s TMR sensors are used in a wide range of applications including automobiles, which are becoming increasingly automated and electrified, industrial equipment, which is often used in environments prone to dust and contamination, and consumer products, which need to be compact and have low power consumption.
Sensing technologies are greatly contributing to the improvement of the fuel efficiency of automobiles. In an automotive engine, crank angle sensors or cam angle sensors are used to obtain information for calculating the optimal timing and amount of fuel injection in the engine ECU (electronic control unit).
Although there are various types of crank angle or cam angle sensors, non-contact type magnetic sensors have become the mainstream because of their insusceptibility to wear or dust. A toothed gear pulsar (pulsar rotor) made of a magnetic material is attached to a crankshaft or cam shaft, and a magnetic sensor to which a magnetic field applied by a bias magnet is contactlessly placed to face it. When the engine starts and the gear pulsar rotates, the density of the magnetic flux from the magnet changes alternately due to the projections and recesses of the gear teeth. The magnetic sensor extracts this as a pulse signal and detects the rotation speed based on the number of pulses per unit time. Because of this mechanism, these sensors are also called gear tooth sensors.
Compared to sensors using a hall element, TDK TMR sensors feature extremely high sensitivity and high output, and realize superior sensing capability as wheel velocity sensors for ABS (anti-lock braking) systems. Moreover, they can also be expected to be utilized as current sensors that conserve energy by controlling charging and discharging of batteries.
In recent years, demand for magnetic sensors has been increasing in fields such as automotive electronic equipment, industrial equipment, and consumer electronics. There is a mindset concerning sensors that, even if characteristics of the elements are somewhat inferior, these can be covered by how they are used (software). However, a sensor is a type of transducer, and still requires good conversion efficiency. In addition, it is predicted that the detection accuracy required of automotive sensors will become approximately twice that of conventional sensors, in order to realize safer and more comfortable driving. TDK TMR sensors are innovative products featuring high output, high accuracy, as well as low temperature drift and low aging deterioration to meet severe and tough market requirement. Owing to these characteristics, they will be able to accommodate future strict accuracy requirements with ease.
TDK is able to meet high-precision sensing needs around the world with TMR sensors that have unparalleled high angle precision and is working on further expansion of the product lineup, so as to support a large variety of applications.